For over 50 years, our thermoforming plastics supplier has been providing outstanding results to a variety of customers. With a range of secondary operations and assembly capabilities, this company offers a comprehensive solution for your vacuum formed plastic manufacturing needs.
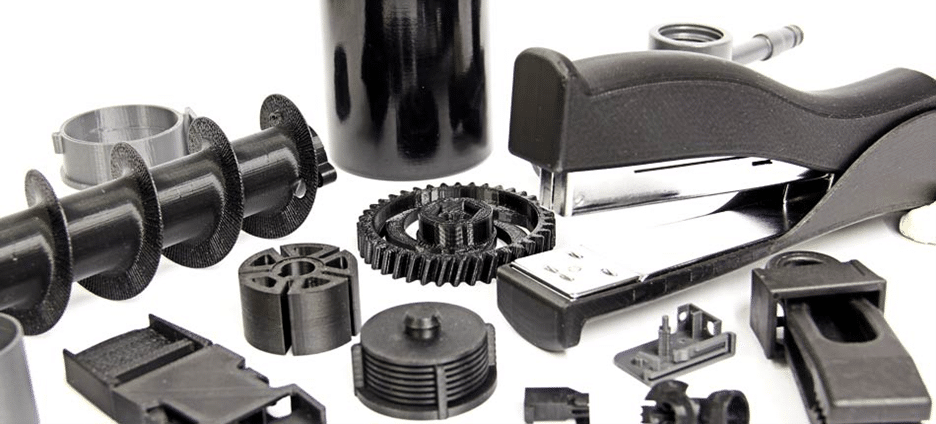
From tanks and frames to high impact displays, our vacuum/thermoforming company’s services cater to a wide array of uses, including:
- Precision trays and secure packaging ideal for the medical sector, food processing plants, and eye-catching retail products. Think of the protection for delicate medical instruments, or the crystal-clear blister packs that showcase your product while keeping it safe.
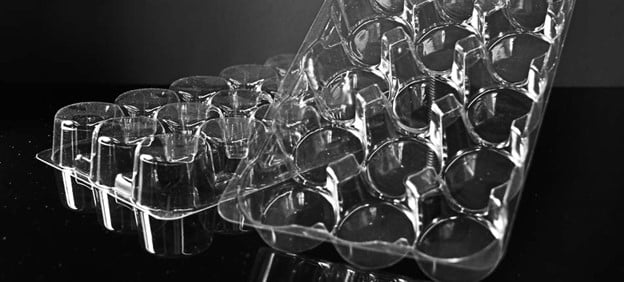
- Robust PVC tanks and frames, designed to withstand the rigors of industrial use.
- Custom-designed equipment guarding and safety shields, providing both functionality and peace of mind.
- Electronic component housing, crafted to exact specifications for seamless integration.
- Striking point-of-purchase and acrylic displays that capture customer attention and drive sales.
- Vital refrigeration components, ensuring that systems operate efficiently and reliably.
- Military and government projects requiring ITAR certification
Interested in prototypes? This supplier has a 3D rapid production system- FDM (Fused deposition modeling) which utilizes 3 different types of plastics (ABS, Polycarbonate, and ULTEM) with a maximum size of 16" x 14" x 16".
In case you have a new product or prototype that eventually might become injection molded, it may be possible to begin with a thermoformed part and convert to injection molding when the new item becomes market approved. Why? You reduce tooling costs by an order of magnitude and design changes can be implemented easily.
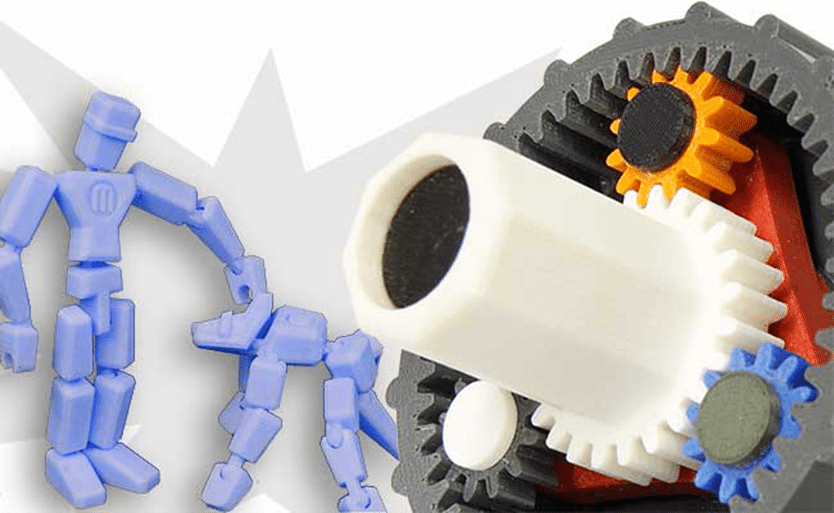
In addition to thermoforming, the company offers a range of secondary capabilities, including:
- CNC machining
- Ultrasonic welding
- Hot air welding
- Solvent bonding
- Silk screening
- Painting
Benefits of Thermoforming
Thermoforming (vacuum forming) offers several key benefits:
Versatile Application: Thermoforming works with many different materials—including ABS, PVC, HDPE, polycarbonate, and other professional plastics. Processes can also be refined to create plastic products with varying thicknesses, textures, and colors.
Rapid Production: Thermoforming equipment is designed to support quick heating and continuous production, which in turn, can help shorten turnaround times and allow for low-volume orders. If you’re still in the design phase, molds can be interchanged with ease to enable rapid prototyping.
Precise Results: Combining air and pressure within a vacuum, thermoforming exerts a careful balance of force that ensures flawless results. Unlike with other plastic fabrication techniques—such as injection molding—thermoformed products deliver a flawless finish that is free of marks, burrs, and scratches. The plastic is also formed so smoothly that all surfaces will remain non-porous.
Cost Reduction: Thermoforming is prized for its ability to minimize manufacturing costs on many different levels. For example, the speed and ease of production make it easy for teams to adjust prototypes without wasting valuable time or materials in the process. Tooling, often using wood molds, is usually much less expensive than other manufacturing processes. Due to its lower energy and pressure requirements, thermoforming is also a much more affordable manufacturing technique than injection, rotational, or blow molding
Choose our thermoforming plastics supplier for your next project and experience the benefits of versatility, speed, and cost-effectiveness. Text or call us (513) 489-5252 and let’s begin!